The Evolution of Integrated Supply: From Piece Price to Total Cost of Ownership
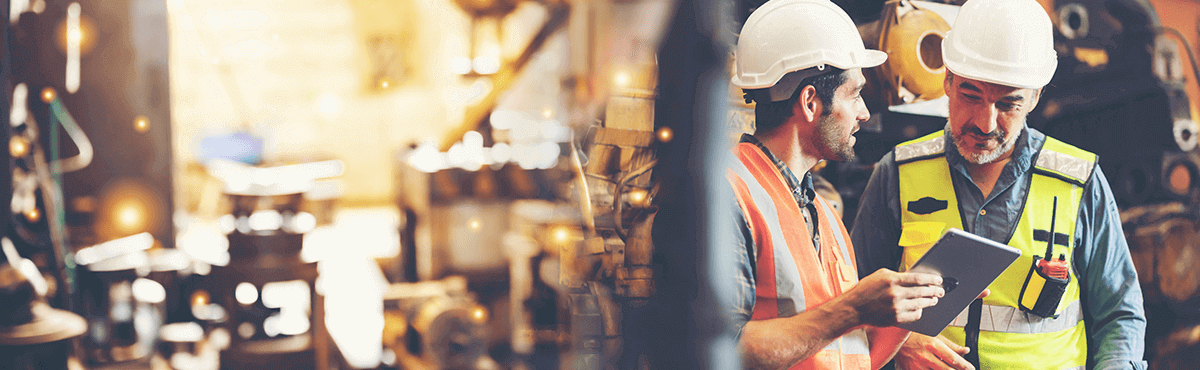
Integrated supply is defined as the management of a supply chain from a single or central perspective. It means that individual projects, departments, or production plants are contained within a single supply chain. It typically refers to the spare parts associated with Maintenance, Repair and Operations (MRO) for manufacturing plants, large campuses, or facilities.
The point of integrating these previously independent supply chains is to introduce shared benefits like better pricing, inventory reduction, and improved maintenance. As a service, integrated supply is typically outsourced to a third party to optimize the total cost of MRO at the point of consumption.
George Krauter, former Vice President for Synovos (now RS Integrated Supply), is credited with developing the concept of integrated supply in the early 1970s. Krauter identified duplications in the supply ordering process when he owned a small industrial distribution company. Those duplications, involving purchase orders, invoices, and even storage, created unnecessary costs.
His solution was called “In Plant Store” and was first implemented at a large manufacturing site in Philadelphia in 1971. He owned inventory in the manufacturer’s storeroom and billed for parts after they were issued or consumed. The entire cycle – purchase order, requisition, invoice — was reduced to one consolidated monthly invoice, eliminating at least three steps in the supply chain.
The idea of integrated supply has evolved since, incorporating technology and digital procurement systems as well as better material tracking, among other advancements. For much of those 50+ years, the focus was on reducing material costs. That is changing.
More attention is now given to how integrated supply reduces Total Cost of Ownership (TCO) by analyzing crucial information such as inventory volumes, frequency of issuance and purchasing patterns. Integrated supply providers also offer substantial savings opportunities on transaction processing, as much as 15% to 25% of overall costs.
Focus on core opportunities
Those cost savings are difficult to achieve in-house. As management consultancy McKinsey reports, “Many companies lack the necessary capabilities to address all of the potential opportunities and capture full value from optimizing indirect spend.” Moreover, is it in a company’s best interests to develop such non-core capabilities even if they could?
Each purchasing transaction, whether a quote request, purchase order, invoice, or something else, has an associated cost. Allowing an integrated supply company to manage that process reduces a company’s transactional burden, both financially and in workforce hours.
“Should you be in that area of the business?” asks Jim Haddow, a supply chain management expert and former professor at the Howard University School of Business, in Washington, D.C. “You should be focusing on your core business and outsourcing other pieces of it, such as Maintenance, Repair and Operations (MRO).”
Move beyond the transactional level
One of the risks with using an integrated supply provider is that the piece price benefits plateau within a couple of years because, states McKinsey, “the transactional focus of many outsourcing relationships tends to inhibit a more strategic optimization approach.” These complementary value-added services and solutions, however, promote the development of a more strategic approach over time.
It is a step-by-step process, explains Costi Campi, Senior Vice President for Global Procurement at RS Integrated Supply. “When we get a client on board, it’s about making sure they continue to receive the goods when they need them,” she says. “We reduce the number of transactions to optimize cost. This is the minimum requirement to gain trust. Then we can introduce additional value propositions.”
Once confidence is established, additional inventory solutions and value-added services can be introduced, including data standardization, enrichment, and inventory optimization, that drive further efficiencies and savings. “We transform from a tactical approach to a strategic one,” observes Campi.
Improve ESG performance
The next step in the evolution of Krauter’s idea, is the inclusion of Environmental, Social and Governance (ESG) performance in purchasing decisions, where both suppliers and end users can improve their ESG standing.
Take efforts to reduce Scope 3 emissions, those that occur in a company’s value chain, as an example. “If providers track information from their suppliers, they can help demonstrate the overall impact of the supply chain and then bring down emissions,” says Haddow. “They are well positioned to do that without the repetition of effort if every company was asking the same question, especially going down the tiers of the supply chain. There’s a lot of value that they can add here.”
ESG will undoubtedly be high on corporate agendas for years to come – as will digital technologies. “Artificial Intelligence (AI) is an opportunity from a data perspective and a transactional perspective,” enthuses Campi. “This is one of the next steps we’re working on. How can we maximize use of AI within procurement?”
It is a question that RS Integrated Supply and other solution providers are asking, even if current operations are yet to be fully optimized. At the same time, it is clear that integrated supply will continue to evolve around ESG and AI, delivering value to industry through fully optimized and more strategic supply chain operations.