BOM and Inventory Optimization: $5 Million Savings Case Study
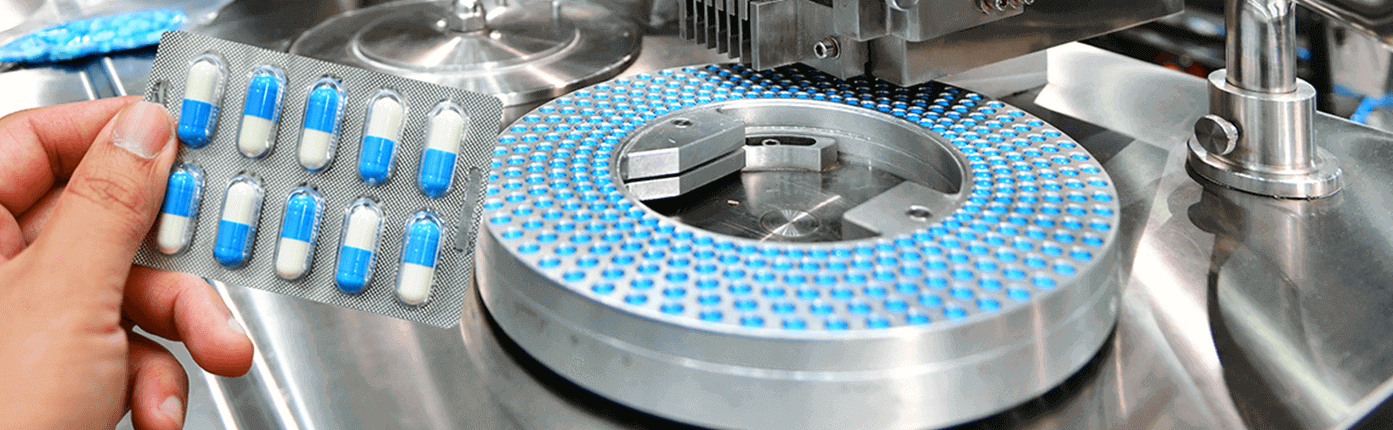
The challenge
A global life sciences manufacturer operating in more than 100 countries was struggling with reliability issues at one of its largest plants.
The company needed to create or update existing bills of materials (BOM) for all equipment, including sub-components, while establishing parent/child relationships. A review showed that BOMs were incomplete, identification structures housed in the company’s system of record were inconsistent, and spare parts were not tied to specific equipment.
The situation created a risk for equipment failure as well as compliance with the Food & Drug Administration (FDA) regulations governing the facility. Both could have disastrous effects on production and profitability.
All BOM projects have challenges. Data often plays a significant role in causing and solving problems.
In this case, the client was unsure what equipment changes were made over the years. There was little confidence in the available technical data, thus requiring walk-downs, where parts were identified in person. The initial project contractor completed a physical walk down on the 22,000 assets identified during the project, eventually sharing the information collected. But that information was lacking in data consistency, as well as the depth of information collected. Much of it had to be redone.
The solution
The project had three main objectives:
- Update or build BOMs for existing equipment.
- Assess MRO inventory to identify reduction opportunities.
- Recommend stocking strategy to better manage inventory growth.
The BOM part of the project identified 20,244 components tied to 574 piping & instrumentation diagrams (P&ID). After isolating and eliminating duplicate items, the total was reduced to less than 18,300 components.
More than 500 P&IDs were submitted for refresh in the client system of record, meaning added information was gathered for that subset. Of the remaining P&IDs, just over half were identified as obsolete or decommissioned parts, with another 34 containing no components within the scope of the project.
The P&IDs resulted in more than 434 system updates. With the improved data accuracy, we mapped the spare parts to the client’s existing material masters within the system of record. Where a material master did not exist, a temporary item number corresponding to the proper component was assigned.
New materials were created as non-stock.
Results further revealed that more than $5 million of inventory value could be targeted for reduction and savings.
Results further revealed that more than $5 million of inventory value could be targeted for reduction and savings.
The results
The MRO assessment resulted in a 15% reduction in inventory value not linked to equipment and a 10% reduction in the number of SKUs. Additionally, an inventory usage analysis also found:
- 54% of SKUs, 41% of the total inventory value, had no usage history.
- 17% of SKUs, 28% of the value, were used within the previous 12 months.
- 11% of the total inventory value had no usage history.
Results further revealed that more than $5 million of inventory value could be targeted for reduction and savings. Adjusting the spare parts turn rate to four, alone, created more than 80% of those potential savings. RS Integrated Supply identified an additional 10% of spare parts not previously included in the client’s CMMS, creating additional value through improved plant reliability.