Boosting Efficiency in Auto Manufacturing with MRO
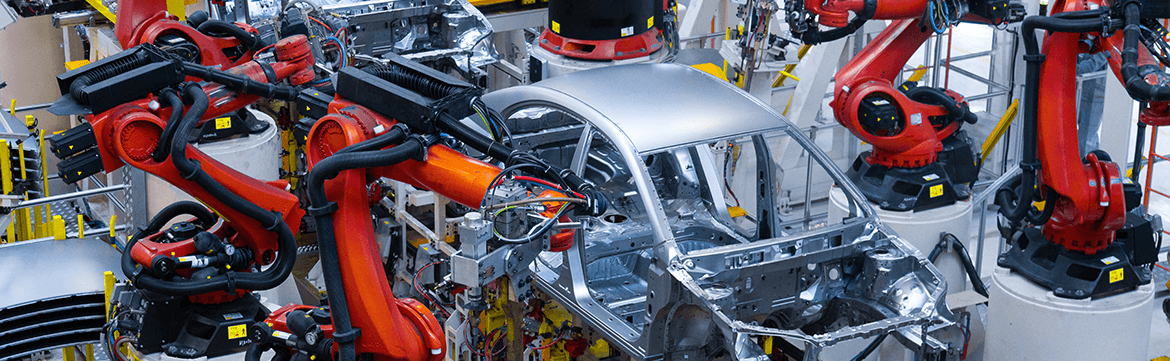
The automotive industry is well known for its precision in the manufacturing plant, with parts and components delivered “just in time” (JIT) to be installed on the moving production line. That reputation has deep roots. While the idea of using interchangeable parts to improve efficiency dates to the Romans, it wasn’t until early in the 20th century that the concept was popularized by Henry Ford when making his Model T.
That process has only been improved upon, as bigger, faster, and smarter technology has brought still newer ways to be more efficient. That thirst is never quenched.
Background
For several years RS Integrated Supply has supported a large global automotive manufacturer with a significant manufacturing footprint in the United Kingdom and EMEA regions.
Our involvement includes strategic product sourcing, transactional buying and processing, storeroom management services, and a delivery framework supporting multiple sites, including a centralised bespoke distribution centre.
Truly integrated within this customer’s manufacturing facilities, RS Integrated Supply manages nine sites, thirteen storeroom locations, over 1000 predefined delivery points, all supporting and maintaining the line side routine and scheduled MRO workflows, through to emergency requirements on a JIT basis.
Meanwhile, the client operates on a strict 24/5 schedule with frequent weekend overtime.
The Challenge
RS Integrated Supply and the customer embarked on a jointly formed project team running a project plan over a nine-month period.
The RS team supporting this customer consisted of 90 people with an additional 15-20 individuals assigned to centralized functions, including purchasing. To ensure its effectiveness, multiple team members across several disciplines were involved in the project.
Through this team all parts were identified and appropriate stock holding requirements for each SKU identified. Then the go-to-market strategies were engaged both with specific Original Equipment Manufacturers (OEMs) and through RS Integrated Supply’s extensive supplier network. These strategies were then enacted through a dedicated team, working with suppliers and OEMs to complete a JIT process flow through to the stores management teams, who, through separate workstreams, created new additional stock holding locations.
Transactions were tracked using RS Integrated Supply’s proprietary MRO technology, maintaining parts visibility throughout the process, despite often long lead times and material shortfalls.
Additionally, the different teams held regular meetings to share status updates on required SKUs, tracking approvals, supplier acceptance, lead time, shipping, and availability, keeping the client thoroughly informed
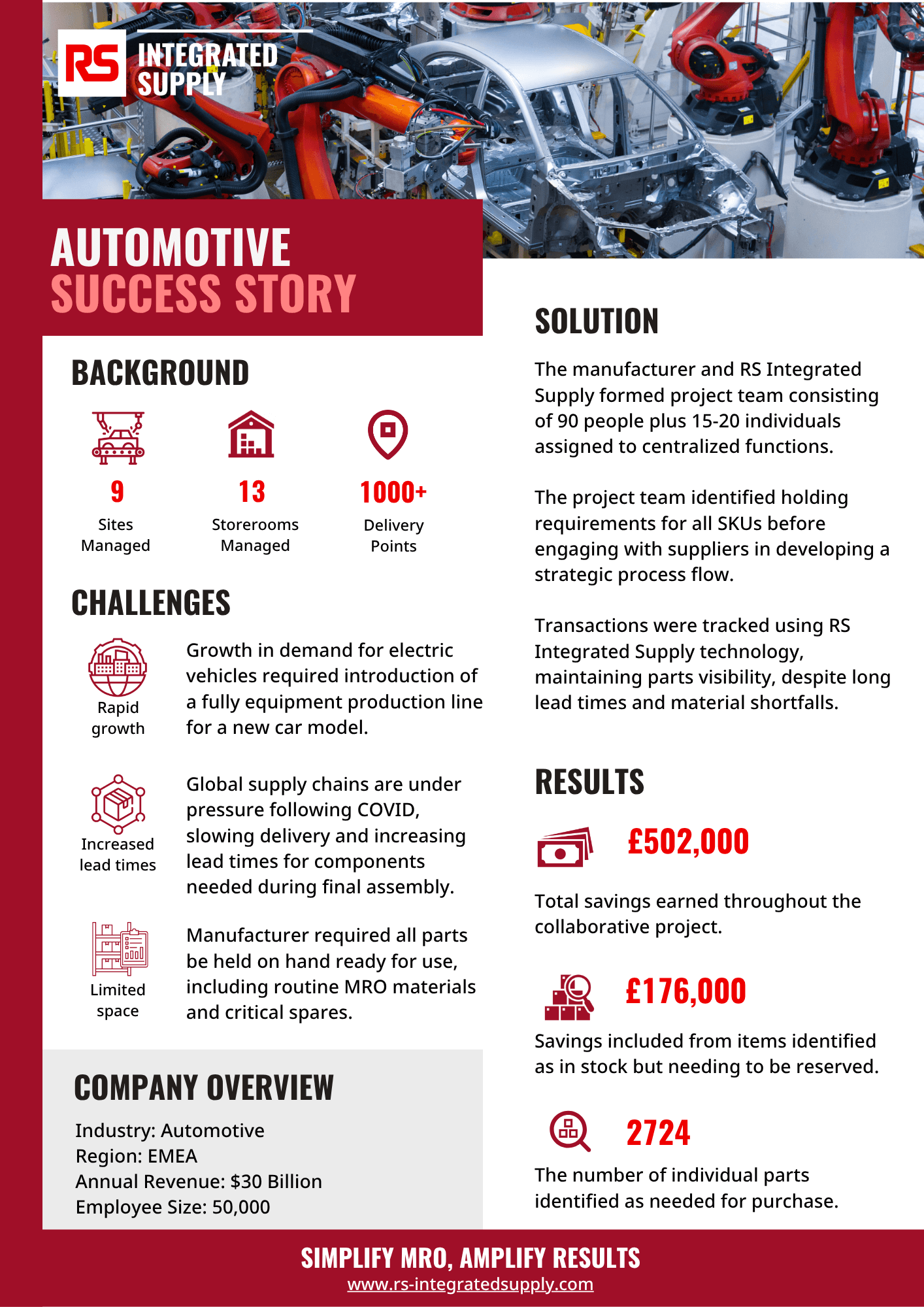
The Solution
RS Integrated Supply initiated a data enrichment program designed to improve overall data quality that would lead to more effective maintenance, reduced downtime, optimized inventory and more.
That program featured SnapPart™, proprietary mobile technology from RS Integrated Supply that leverages text and voice recognition, web search, and bar code scanning for rapid parts identification.
Typically, the process begins with an analysis of the client’s initial data pack. In this case, that pack had virtually zero reliable information, i.e., manufacturer name, manufacturer part number, supplier name and part number, etc. That lack of detail triggered a more manual approach where the RS team conducted a wall-to-wall inventory of more than 3,000 parts, using SnapPart™ to capture the required data around manufacturer name and part number, categorization and product images
Once collected, the information is cross checked using global IDs to accelerate the enrichment process. The data collection team then reviews the improved data to ensure heightened accuracy.
Finally, the data is uploaded into the client’s MRO software system, from which procurement and maintenance can order materials, issue work orders and track progress.
result
Throughout the project, reporting and progress visuals and milestone forecasting took place, including parts for which an additional critical focus was applied. This provided the customer with transparency and outlook visibility throughout the period.
During the project and through a detailed assessment of existing inventory, it was identified that a volume of spare parts was already available in the RS-managed storerooms that could be moved through internal transfer between facilities to preserve budget costs. This action alone generated £176K in cost avoidance for the customer.
The project overall was delivered in the timescale, with all outlined risks captured and managed, ensuring that not only could this customer maintain its orderbook commitments, but through the collaboration between the two businesses, an overall budget savings of £502k was achieved.
- Total project budget assigned: £2,560m
- Total Budget used: £2,060m
- Total savings achieved: £502k
- Includes items identified as in stock but needing to be reserved £176k
- Number of individual parts identified for purchasing: 2,724
The client remains among RS Integrated Supply’s longest active accounts.