Streamlining Operations: A Food Manufacturer’s Success with an Integrated MRO Storeroom
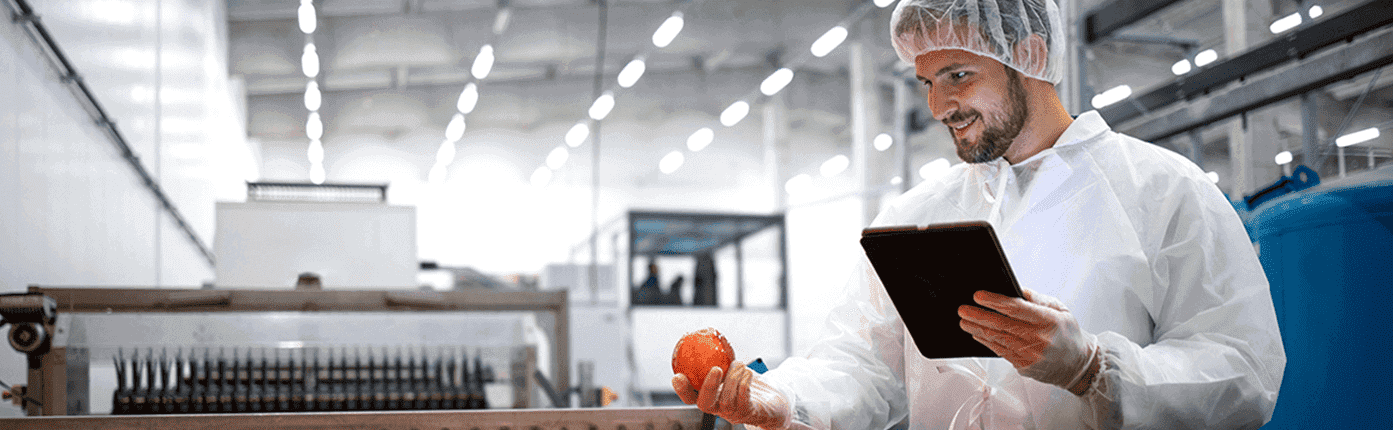
The challenge
A multi-billion-dollar food manufacturer used a reactive approach to maintenance – allowing assets to run until failure before stepping in to make repairs. Although maintenance team members were great “firefighters,” the approach failed to improve plant reliability.
To change from a reactive to proactive plant, the manufacturer invested in an asset management system. But internal resistance to change proved too much to overcome, resulting in a failed implementation. Disconnect between maintenance and the MRO / indirect materials storeroom was a major factor in the lack of success.
The solution
A second initiative, this time involving a third-party MRO integrated supply services provider, was launched, and backed by the company’s leadership team.
That leadership support was a significant advantage as RS Integrated Supply collaborated with those key leaders to tie storeroom operations into stronger plant reliability and better master data management.
This time, with consultation from RS Integrated Supply, the client expanded the project goal beyond asset performance to include overall maintenance effectiveness.
It was a decision that directly impacted overall plant performance. A set of objectives and key performance indicators were established, the site benchmarked, and storeroom operations were integrated into the solution.
The stores team led by a local site manager and corporate Program Manager put together an improvement action plan that included:
- Application of Lean principles to the storeroom
- Wall-to-wall inventory
- Elimination of duplicate parts
- Elimination of co-mingling of parts
- Identification of reorder point re-evaluation opportunities (e.g., min /max levels)
- Value Stream Map of Maintenance Work Process and dependencies on stores
- Elimination of constraints
- Establish Standard Operating Procedures (SOPs) for processes like Material Receiving, Put Away and Issuing
- Establishing storage processes and procedures for all paperwork and setting up “a place for everything and everything in its place”
- Cycle Counting
- Contribution to Maintenance (culture change element):
- Developing Master Equipment List (MEL)
- Identifying critical equipment and related spares
- Developing Bills of Material for critical equipment
- Participating in Failure Mode Effects Analysis (FMEA)
A set of objectives and key performance indicators were established; the plant was benchmarked, and storeroom operations were integrated into the solution.
A set of objectives and key performance indicators were established; the plant was benchmarked, and storeroom operations were integrated into the solution.
The results
Plant maintenance was transformed into a well-planned operation utilizing a fully integrated MRO storeroom to deliver improved data, daily service levels, and asset reliability performance.
There were three main takeaways from the project:
- When finished, the plant experienced a maintenance transformation by establishing a proactive maintenance process that ultimately led to less downtime and greater maintenance efficiency.
- The project demonstrated the necessity for partnership between maintenance and stores operations to achieve success
- Specific processes and measurement criteria followed to implement maintenance improvement.