Saving $90,000 Annually with Point-of-Use Inventory: A Pharmaceutical Company’s Case Study
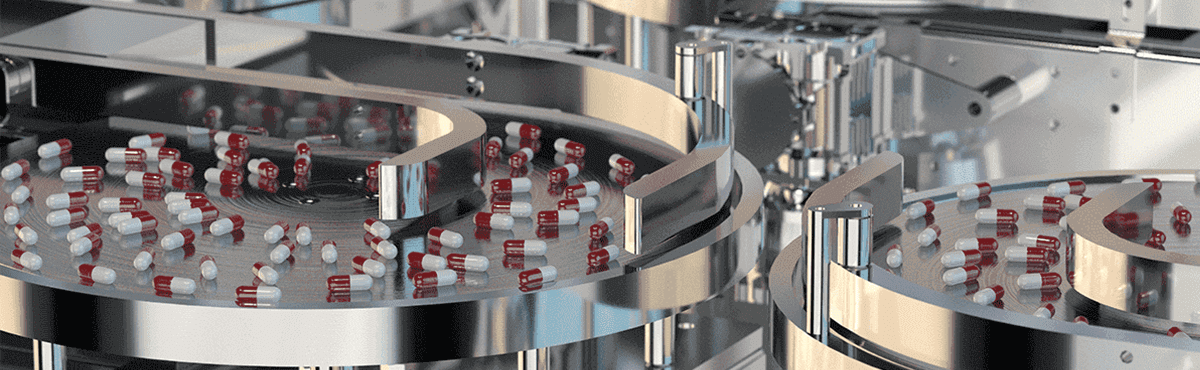
The challenge
A large, multinational pharmaceutical company realized its inventory deployment process, including the inventory storeroom location itself, was creating high indirect material costs because of lost productivity.
The facility used a manual kitting process for work orders. Technicians were responsible for selecting required materials matched to each assigned work order. Materials were stored in bins located throughout the facility.
However, because products were stored in multiple locations, technicians were, at times, required to travel 40 to 45 minutes to secure the necessary items.
The process of collecting materials prolonged the required maintenance time.
The solution
Working with the client’s Six Sigma champion, RS Integrated Supply recommended a point-of-use or vending solution.
In this case, the “Super RoboCrib” carousel was vending unit with locker capabilities was the recommendation.
When strategically placed throughout the plant, such units reduce walk-around time for technicians while enabling better tracking of product usage.
The Super RoboCrib, because of its locker capabilities, holds enough inventory to cover up to two weeks. It has tremendous capabilities, including several required by the Food and Drug Administration such as Lot control. Each unit is checked weekly and re-stocked as needed.
“These are well-built and reliable machines,” said Tim Ames, manager, Storeroom Technology, RS Integrated Supply. “As long as you spend a few hours each month maintaining them, they won’t cause any problems. They are always there, waiting to be used.”
With this new process in place, technicians no longer need to walk across the campus to get parts; the kits are completed and issued using the locker capabilities of the Super RoboCrib.
This particular site is saving more than $90,000 annually …. The savings delivered 100% ROI on the project in less than 12 months.
This particular site is saving more than $90,000 annually …. The savings delivered 100% ROI on the project in less than 12 months.
The results
Technician trip time was reduced to six minutes from 40 to 45 minutes, saving more than 300 miles in foot traffic and seven hours each week. This particular site is saving more than $90,000 annually, not including the increase in man-hours available for wrench time. The savings delivered 100% ROI on the project in less than 12 months.