Transportation Manufacturer Improves Efficiency with $1M+ in Savings from MRO Supply Chain
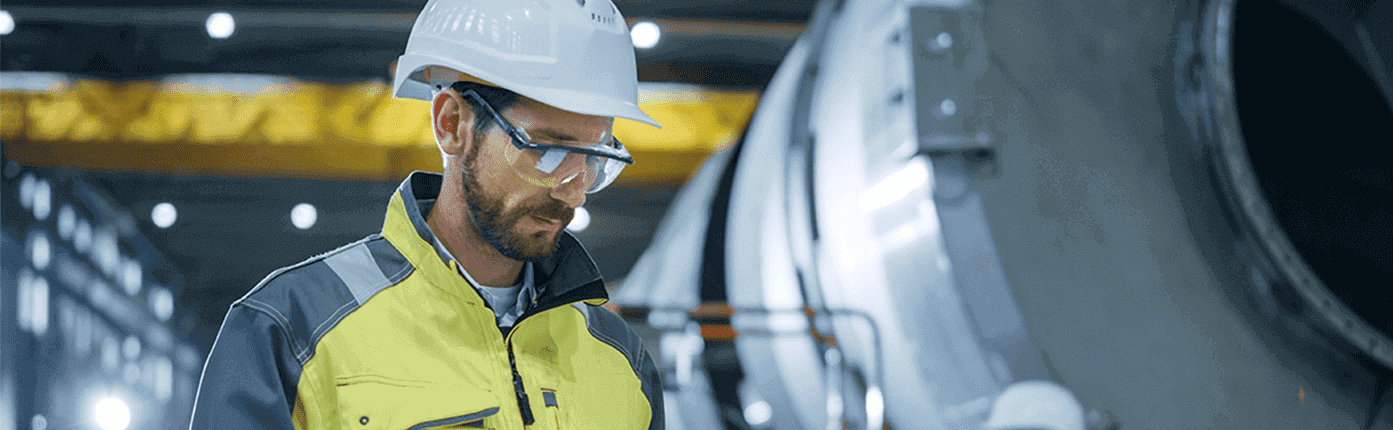
The challenge
A new leadership team at a large US transport manufacturer uncovered deep-rooted issues with the company’s supply chain. Problems included lack of planning, no insight into inventory value or location, and negative or unknown Key Performance Indicators for measures like on-time delivery and stock fill rates.
Multiple buildings and stockrooms were scattered across a large site, with each building involved in different elements of production. Each department was acting independently, sourcing its own inventory, with little regard of what was going on across the company.
MRO was out of control; inventory rotted in sealed containers across the facility; and there was a culture of reactiveness which led to production delays.
Enough was enough: the manufacturer appointed a contractor to address the issues, but they could not get a handle on the situation. After this failed attempt, the company enlisted the help of RS Integrated Supply.
The solution
The solution we rolled out touched on all aspects of inventory management. Over six months we identified, counted and organized the manufacturer’s existing inventory. A big win was the introduction of an Enterprise Asset Management (EAM) system to catalogue more than 19,000 Stock Keeping Units (SKU) totalling more than $15 million. The system was used to track planned maintenance activity and tie requisitions, work orders and invoices to those plans.
We identified a large, highly secure facility close to the site to store materials, bringing them all under one roof. We designed a process to deliver materials to the right building, as well as strategically placing vending machines across the site to enable faster parts delivery and availability. All transactions are now tracked and automated for restock through our SYNC™ technology platform.
We reorganized the storeroom, putting all related items in the same location, so employees could easily find the parts they needed. We introduced other practical solutions including the use of Vidmar® cabinets and shelving units to hold assorted parts, organized according to industry best practices and properly indexed for quick reference.
We gave the client better inventory control and visibility, showing all materials in a single system, and helping them access the materials they wanted, when they needed them.
We gave the client better inventory control and visibility, showing all materials in a single system, and helping them access the materials they wanted, when they needed them.
The results
We delivered a full end-to-end MRO supply chain management program including:
- Master data analysis: a review of all spending data, frequency, and pricing.
- Strategic sourcing: identification of preferred suppliers and savings opportunities.
- Inventory optimization: better visibility of assets across the company.
- Storeroom management: improved tracking of materials and utilizing inventory.
- MRO technology platform: deployment of an EAM system with cleansed customer data, enabling real-time evaluation of materials, purchases, work orders, budgets, and maintenance effectiveness.
Three years in, the program has delivered savings of nearly $1 million as well as improved efficiency.
The client has expanded production of its high-end and complex finished products, adding more machines and maintenance requirements. We have consistently earned the client’s highest-ranked contractor award and we have been consistently rated ‘excellent’ for total value, quality, delivery, and customer support.
We have now launched our MRO program at two additional client sites, with plans to roll out to five further sites across the USA.